By Lyra Fontaine
Through innovative capstone projects, ME students worked with community members to design a mobility system that could adapt to varying energy levels and abilities.
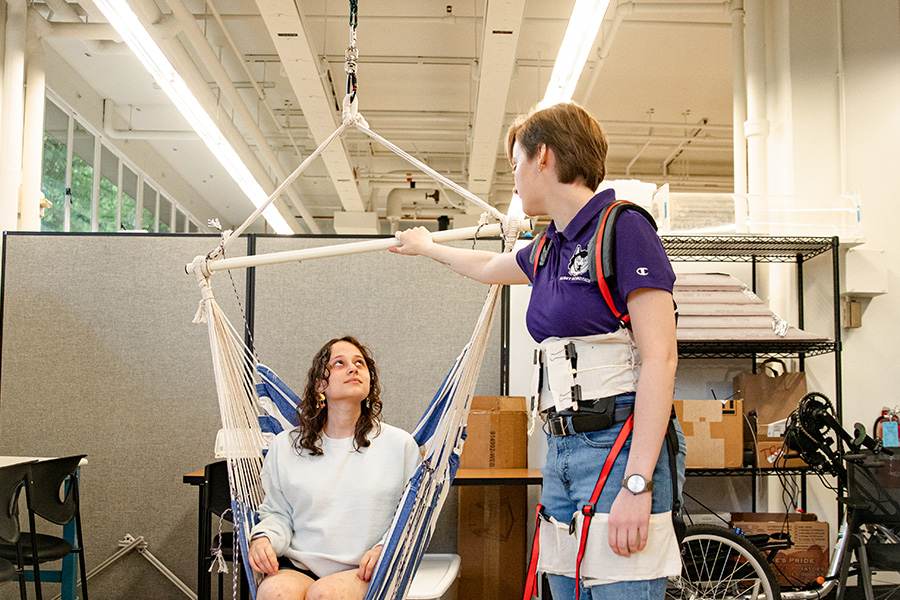
Monica Santiago (BSME ’24) and Tori Landrum (BSME ’24) were part of a team that designed a harness-based support system attached to an overhead frame structure. Other members were Megan Lee and William Chuang. Photo by Jorge Azpeitia/UW Photo.
The goal is to create a holistic physical environment that is beautiful, affirming and adaptable to individuals’ needs as they change over time”
The students gained valuable experience working with clients and collaborating across multiple teams as they designed, fabricated and tested prototypes for a system that could help people with limited mobility.
“The goal is to create a holistic physical environment that is beautiful, affirming and adaptable to individuals’ needs as they change over time,” says Mary Meyer, a Seattle-area fitness trainer and coach who, along with architect Stan Chiu, collaborated with students on the projects. “This includes a mobility system that would inspire individuals to stay active and mobile while being supportive.”
Meyer is a lifelong athlete who has competed in collegiate swimming, skiing and triathlons. While she continues to be active, at age 45, she was diagnosed with severe spinal multiple sclerosis (MS). Many people with MS, a chronic disease that affects the central nervous system, experience fluctuations in their symptoms, such as fatigue and muscle weakness.
Unlike many existing mobility systems that focus on wheelchair use and may appear obtrusive, Meyer envisions a home that provides adaptable support for people with limited mobility whose energy levels might vary each day, and that could help people as they age. This system allows individuals to choose how much support they need at any given time.
“I’m challenged enough outside, and now I’m coming inside and want to relax, feel safe and feel good about who I am and where I am,” Meyer says.
After working with the UW Human Centered Design and Engineering department on the design, Meyer and Chiu turned to ME to see the feasibility of manufacturing a prototype of an in-home mobility system.
This became the Adaptable House Project, which includes four 2023-24 ME capstone projects. One team was tasked with designing and defining requirements for an overhead mobility system. Other teams focused on creating a harness and chair with adjustable support, ensuring users could use the system without swaying, and working on the system’s lifting control to prevent falls.
An adjustable harness system
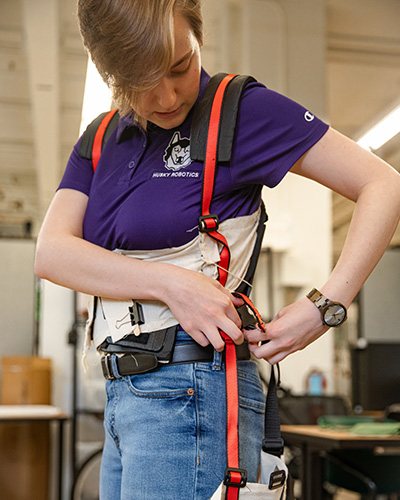
Tori Landrum (BSME ’24) adjusts an early prototype of the harness. Photo by Jorge Azpeitia/UW Photo.
One team designed a harness-based support system attached to an overhead frame structure, with multiple levels of support for people with mobility-based disabilities. To increase users’ independence and confidence, the goal was to make the system safe, durable, aesthetically pleasing and comfortable for long periods of wear.
“Mary wanted to emphasize empowering the user, so we worked to make the harness and chair feel positive and not debilitating,” says team member Monica Santiago (BSME ’24).
For about a month, the team brainstormed harness and chair ideas with Meyer, Chiu and their faculty mentor Eli Patten, ME capstone director and assistant teaching professor. Meyer’s needs included back and abdominal support.
For early harness prototypes, the students got creative and used cardboard, 3D-printed material, foam and more. For their later prototype, they used a non-stretchable cotton blend material with nylon webbing, padding on the shoulders, 3D-printed plastic to provide structure in the back area and velcro to close the harness. The chair they selected for the full support mode was a hammock chair fitted with a footrest and a foam back rest.
The team members learned a variety of skills, from budgeting, understanding the user experience and cooperating with other sub-teams to using a sewing machine and testing material strength.
“We emphasized the user experience by working to understand Mary’s needs and considering colors, fabric feel and more,” says team member Tori Landrum (BSME ’24). “We applied ME fundamentals to things we’ve never done before, such as testing fabric and velcro using a tensile testing machine.”
The team found that the frame and harness support up to 300 pounds for all system modes, and users can comfortably wear the system for more than four hours. To test the comfort of the harness, Landrum wore it for a day, including to class.
“This project, which promotes mobility in households for individuals with disabilities, aligned with my passions and seemed really unique,” says Landrum, who’s been involved in undergraduate research focused on biomechanics and human movement. “I wanted something that felt personal and had a direct impact.”
“One reason I went into engineering was to tangibly benefit people’s lives,” Santiago says. “This has been a good way to give back to the community.”
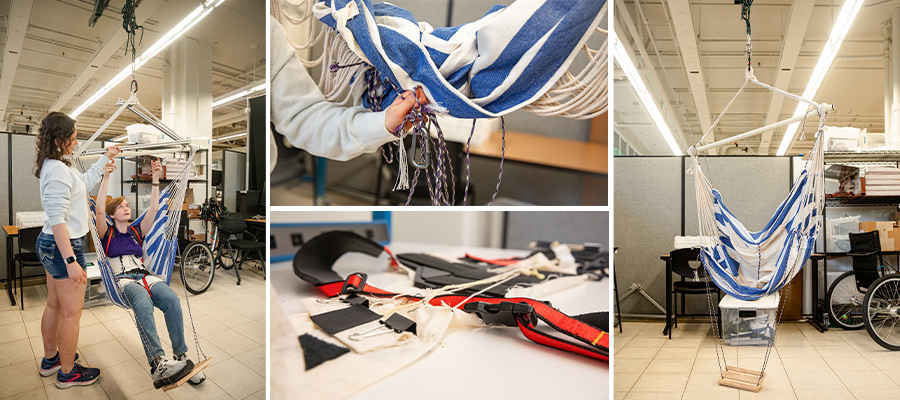
Monica Santiago and Tori Landrum showcase the hammock chair and an early prototype of the harness. Photos by Jorge Azpeitia/UW Photo.
Lift control using mechatronics
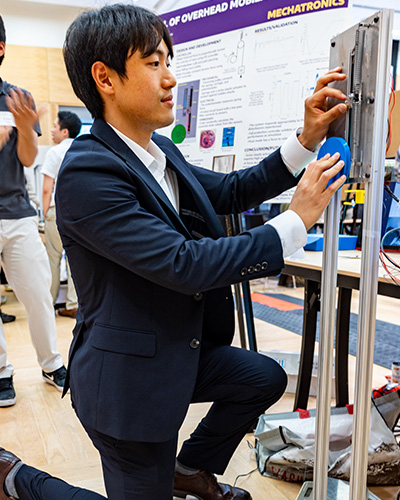
John Shim (BSME ’24) demonstrates how the prototype consists of a motor that provides rotational energy and a pulley that redirects the rotational power to lift the user. Photo by Matt Hagen.
The capstone team responsible for the overhead mobility system’s lifting control demonstrated how to implement adaptable body weight and fall protection systems to aid and empower individuals with mobility impairments.
“If the user is wearing the harness, the prototype we built can adjust their body weight by taking some weight off them,” says team member John Shim (BSME ’24). “Such a dynamical system will provide optimal mobility support tailored towards each individual.”
The lift control system has three different modes: fall protection, body weight support and float. Fall protection catches a falling user and automatically activates when the user exceeds a specified velocity threshold. In float mode, users are suspended in the air, allowing caretakers to move them around the room with a gentle push or pull. Users could transition between various modes and modify the level of body weight support by pressing a button on a remote control.
After talking with Meyer and Chiu to understand the project needs, the team members modeled the system with math and physics concepts, says Shim. Next, the students built a prototype consisting of a motor that provides rotational energy and a pulley that redirects the rotational power to lift the user. They incorporated a series elastic actuator by adding a spring in between the motor and the user. This allows the system to absorb shocks to keep them safe from sudden movement or a fall.
Shim and his teammates successfully tested their design. Eventually, a scaled-up version of this prototype could make it easier for users to move around their homes.
Joseph Garbini, Professor James B. Morrison Endowed Chair of mechanical engineering, was the project’s faculty mentor. Other team members were Everett Hirano, Keita Yamamoto and Maya Larson.
“This project was a perfect fit because I wanted to get involved in the medical industry and help others using technology,” Shim says. “I’m grateful for the valuable mechatronics skills we learned from this project and Professor Garbini. The skills we learned, such as modeling dynamic systems, running simulations properly, professionally presenting our experimental results and collaborating with others, will be invaluable as I pursue a career in engineering.”
Expanding possibilities
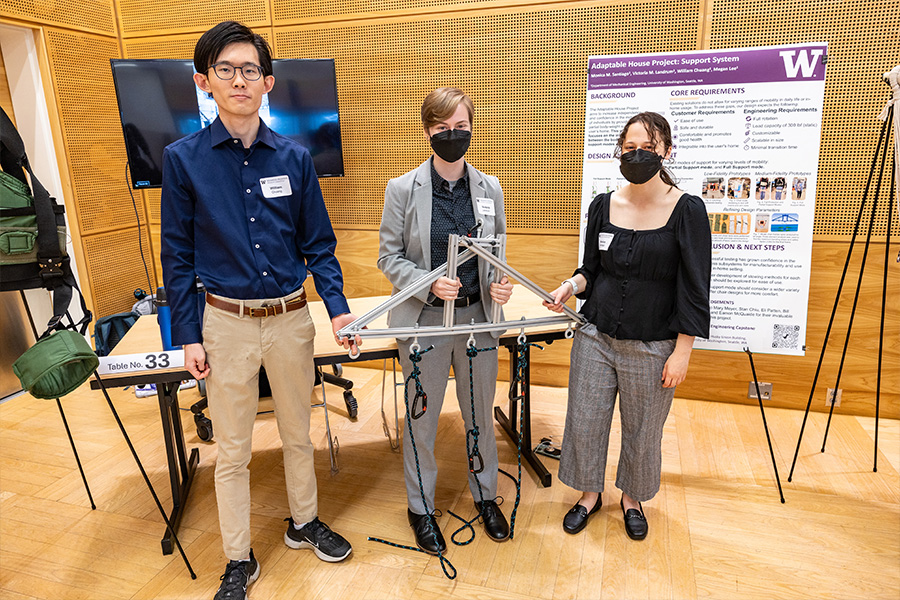
The team who developed the support system at the ME Capstone Expo. Photo by Matt Hagen.
Since the testing showed that the mobility system is feasible, the students provided ideas for improvement so that future capstone teams could build upon their work.
“It’s been energizing to watch the groups collaborate,” Chiu says. “Some teams moved ahead and asked us specific questions, which felt like a designer-client relationship. With other teams, we co-created the prototypes, which was deeply collaborative.”
Chiu recently injured his back, which made the project even more personal to him. “Injuries and aging happen to all of us,” he says. “A mobility system like this could extend all of our possibilities.”
Similarly, Meyer is guided by questions such as “Can we make life a little easier for people? Why don’t we have houses that we can grow old in?”
“Working with the students is really encouraging as it helps us continue the project,” Meyer says. “I love that it’s such a real-life experience. Seeing it all come together has been exceptional.”
Originally published June 27, 2024