By Lyra Fontaine
ME researchers found a solution to mitigating the noise caused by the SR 520 floating bridge’s expansion joints.
The Evergreen Point Floating Bridge (SR 520 bridge), which reopened in 2016, has expansion joints that created noise problems. They discovered the main sources of noise were the resonance of the air within the expansion joint gaps and the vibration of the car tires. Researchers in the ME department designed, tested and recommended strategies that successfully reduced the noise caused by the bridge.
Like many bridges around the world, the Evergreen Point Floating Bridge (SR 520 bridge) has expansion joints that allow it to expand or contract to adapt to environmental changes, such as changes in water level, without causing structural damage. However, expansion joints can create noise problems. When the new SR 520 bridge opened in 2016, the constant sound of vehicles driving over the bridge’s expansion joints became a nuisance for homeowners in the surrounding area.
Researchers in the ME department designed, tested and recommended strategies that successfully reduced the noise caused by the bridge.
“We lowered the noise level about 70 percent or 10 decibels,” says ME Professor Per Reinhall.
The research team is now gearing up for the next phase of the project with the Washington State Department of Transportation (WSDOT): developing and testing materials to extend the durability of the treatment.
Solving the noise problem
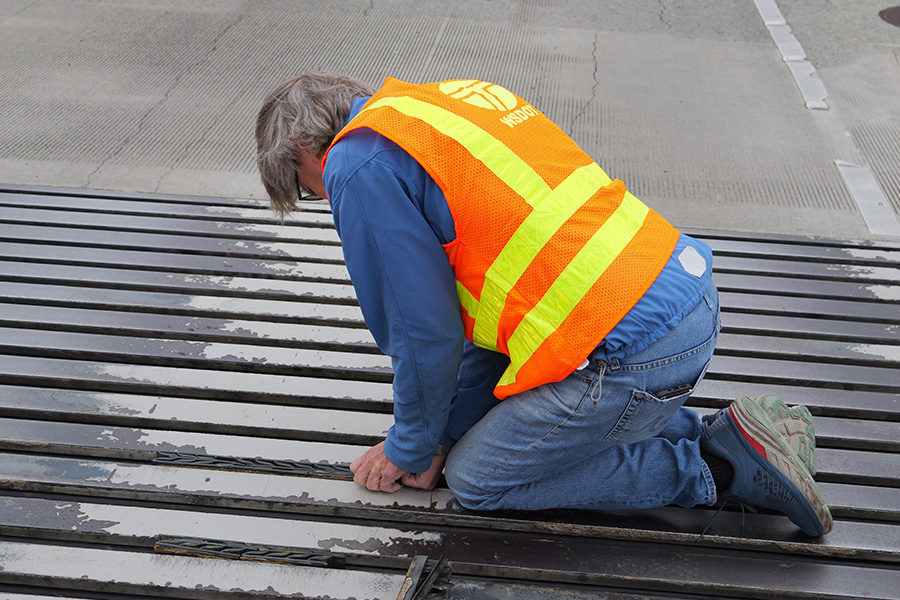
ME Professor Per Reinhall fitting the chevron material in between the beams of the SR 520 bridge.
The project began in 2018, when WSDOT reached out to Reinhall, who has expertise in removing noise in marine environments. His research team measured the noise in the neighborhood by setting up microphones, and investigated the causes of the noise and how it spread. They discovered the main sources of noise were the resonance of the air within the expansion joint gaps and the vibration of the car tires.
ME Ph.D. student Sawyer Thomas became interested in the project since it involved materials and mechanisms that expanded and contracted to accommodate movement. Thomas is now a graduate research assistant for the project.
“In my Ph.D., I am focused on structures that can shape-shift, bend and move in interesting ways,” Thomas says. “This project also appealed to me because it has a real-world application that will be useful when it’s implemented.”
The research team brainstormed ideas for how to solve the noise problem. Thomas then worked on ideation, designing, prototyping and testing of different structures that could fit between the expansion joints to mitigate the sound.
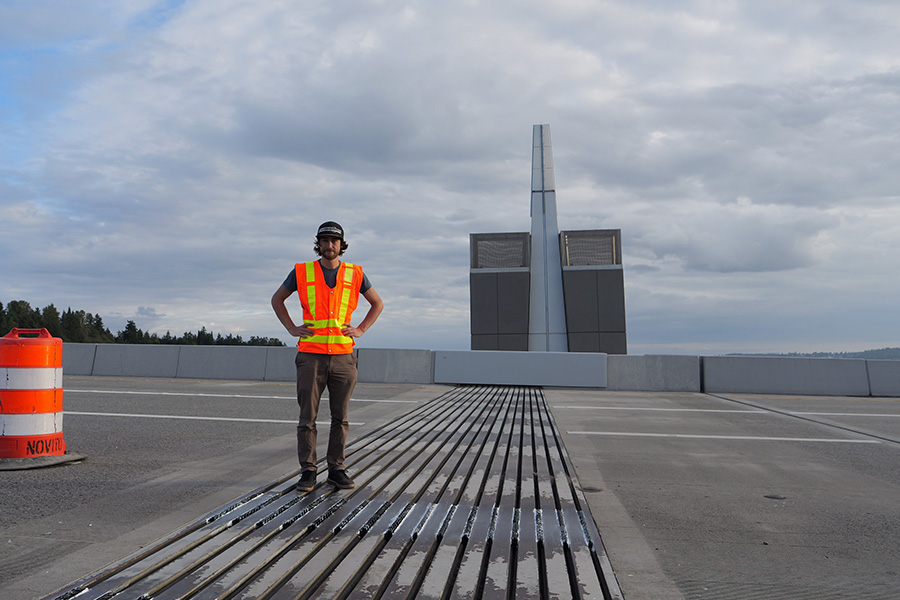
Ph.D. student Sawyer Thomas standing on the SR 520 bridge next to the installed chevron supports.
“The material is ideally supposed to support the weight of a car partially to reduce the impact of the tire on the beam. It was a challenging design problem because there were such extreme constraints,” Thomas says. “We needed something that was able to have that range of motion while being durable enough to withstand thousands and thousands of cars.”
The team decided that a chevron rubber-like material that can change from 1 inch to 3.5 inches in width would be the best option. The material fills in the gaps of the beams that create noise. They 3D-printed prototypes for lab testing and then ordered molded parts for the bridge test.
After validating their simulation of the bridge, the team moved forward with installing the materials on one lane of the bridge and testing the treatment’s performance through capturing audio recordings before and after installation.
“We glued the molded system in place between the beams and filled it with foam,” Reinhall says. “It turned out to be very effective in removing the noise.”
Next steps
The treatment held up well for several months, then started to disintegrate. For the third phase in the project, starting in June, the researchers will explore how to make the treatment more durable for a longer-term solution. They will then follow the treatment for two and a half years to determine its success.
The researchers will experiment and test different materials, including a mixture of natural and synthetic rubbers with embedded fibers to strengthen it – similar to the material used to create tires.
“We know that our solution successfully took care of the noise,” Reinhall says. “Now, we have to make it last about two to four years.”
Originally published March 13, 2023